DMG MORI with linear motor driven CTX beta linear machine allows MD Drucklufttechnik to machine parts with the highest precision and dynamic performance
MD Drucklufttechnik has a history of more than 100 years of pneumatic tools and pneumatics. Today, headquartered in Stuttgart, it was evolved in 1983 by the Mannesmann Group, which has been producing high quality handheld pneumatic tools and motors since its inception. In 2010, MD Drucklufttechnik purchased a total of seven lathes and automatic lathes from DMG MORI to meet the high quality and flexibility required for their own production of parts. Five of the machines are also equipped with high-precision, wear-free linear motor drives.
“The high reliability, high quality products and a comprehensive customer-oriented culture made in Germany are the main factors for our successâ€, and Claus-Werner Bay defines MD Drucklufttechnik's corporate culture. He runs this traditional business with his father, Werner Bay. Long-term experience and development strength make this Stuttgart company achieve high customer satisfaction. It is important to recognize customer requirements: “Not only for the handheld pneumatic tool business, but also for the customized solution business of machine and system manufacturer customers.†In short, their highest quality standards are used in many industries. The general manager of the company also noted the need to respond quickly to maintain competitive advantage, especially the competitive advantage of dedicated solutions – because such business accounts for about 40% of the total order. “Our short process played a key role in this. When other companies were still busy making quotes, we were ready for the first prototype.â€
Claus-Werner Bay believes that the company's rapid development and rapid production are based on the know-how of the company's approximately 60 employees: "High-quality employees are the most critical." This is especially true after 2010. The reason: At that time MD Drucklufttechnik started manufacturing itself. “When the economy is in recession, we realize that the difficulty of relying too much on suppliers may increase, so we decided to perform some of our production tasks,†recalls the company’s general manager. This increases our flexibility and ultimately allows the company to control critical components.
A wide range of models to produce a wide range of parts
Since then, MD Drucklufttechnik has been produced with DMG MORI lathes and automatic lathes. “One of our suppliers has used the TWIN series of machines at the time, so it is easy to transfer to our own production,†says Claus-Werner Bay, explaining why he chose the machine tool company. With the development of the business, the machine shop has now added five CTX lathes and two SPRINT series automatic lathes. Volker Westermann, Technical Manager of MD Drucklufttechnik, introduced the reasons for choosing these machines: “We are going to produce 1000 larger batches of parts with SPRINT automatic lathes. CTX beta 1250 TC is suitable for machining complex car/milling parts, otherwise these parts We have to produce outsourced.†For smaller and medium batch parts, the CTX beta 800 linear and CTX 420 linear are used for turning.
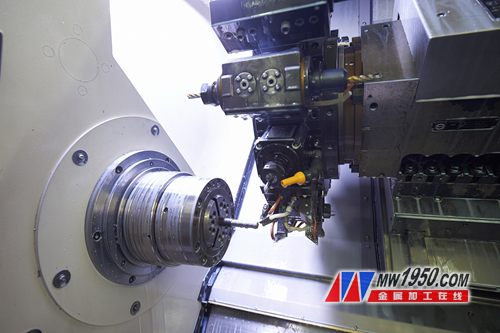
The linear motor drive of the three CTX beta 800 linear lathes ensures extremely high dynamic performance and extremely complex machining of complex workpieces.
Most of the parts produced by MD Drucklufttechnik are high-precision and often complex parts, so the X-axis and Z-axis of the CTX linear lathe and the X1 and X3 axes of the SPRINT 42|10 linear are particularly important for linear motor drives. This technology allows the machine to process with accelerations of up to 1 g. "Because of its dynamic performance and higher positioning accuracy, we have increased productivity," Volker Westermann said. High precision positioning is very beneficial for high quality. High-quality engineers and technicians believe that another advantage of linear motor drives is that they are wear-free: "This is extremely important for the accuracy and reliability of the feed axis."
Machine reliability is critical to MD Drucklufttechnik. “The loss of machine downtime is irreparable, so we need service partners to respond quickly when problems arise, just as we respond quickly to customer requests,†says Clause-Werner Bay. In this regard, DMG MORI gives us good service, in part because it is closer to Leonberg.
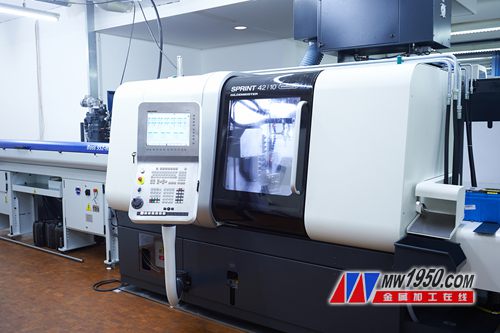
MD Drucklufttechnik's two SPRINT 42|10 linear automatic lathes, one of which is equipped with a bar feeder to produce up to 1000 high-volume parts.
Brass Plated Steel Wire Rope
Brass Plated Steel Wire rope is the main substrate
for the production of Diamond Wire Saw. Firstly,the artificial
diamond particles are consolidated on the metal steel body to make diamond
beads,and then the beads are strung on brass plated
Steel Wire Rope. The special molds and equipment are used for glue injection
molding, and fixing to make a strip-shaped flexible diamond cutting tool. The
emergence of Diamond Wire saw mining technology in stone mines is a revolution
in stone mining. The technology for stone mining has a wide adaptability, strong
function, high efficiency, deep mining depth, and can be cut in various
directions such as vertical, horizontal, and inclined planes, high yield, low
comprehensive cost, safety and environment protection, and no noise in wire saw
mining. No dust and other advantages. In today`s increasingly scarce resources
and soaring oil prices, mining granite with wire saws has significant economic
and social benefits.
Brass Plated Steel Wire Rope,Brass Plated Steel Cord,Brass Plated Steel Wire Saw,4.9Mm Brass Coated Steel Wire
Jiangyin Baoneng Precision New Material Co.,LTD , https://www.baonengwire.com