Service Phone 13760177211 Wu Peng Website:
First, Shenzhen Chuangshengyuan company series filter press implementation standards:
1. JB/T 4333.1-2005 "Type and basic parameters of chamber filter press and plate and frame filter press"
2. JB/T 4333.2-2005 "Technical conditions for chamber filter press and plate and frame filter press"
3, JB/T 4333.3-2005 "car filter press and plate and frame filter press filter plate"
Second, the main components of the box automatic filter press
a) Rack components
2 The frame is the basis of the whole set of equipment. It is mainly used to support the filter mechanism and the pull plate mechanism. It consists of the connection of the thrust plate, the pressing plate, the base, the cylinder block and the main beam. The main beam, the pressing plate, the thrust plate, the base, the hydraulic motor, the pull plate device and the pull plate transmission mechanism are processed by the integral steel plate, and have extremely high strength, in addition to the self-weight of the supporting device itself, The weight of the material entering the filter press.
2 The main machine is designed and manufactured by machine, electric and liquid integrated and machine, electric and liquid. The rack, hydraulic and electronic control systems are independent unit structures for easy maintenance and inspection. It not only avoids the erosion of the working environment on the hydraulic and electronic control systems, but also realizes remote control with the central control room.
2 The whole machine frame adopts all-steel welded structure. After the heat treatment after welding to eliminate the internal stress, the finishing is performed.
2 The main beam is made of Q235-A material. In order to increase the anti-twist and tensile strength of the main beam, a combined structure is adopted especially for the main beam production. That is, the two rectangular hollow square steels are welded together to make the anti-twist and tensile strength of the main beam increase reasonably.
b) pressing mechanism
2 The pressing mechanism consists of the cylinder block, the piston, the piston rod, the electrical contact pressure gauge and the oil pipe that opens into the cylinder block. The cylinder is powered by a high pressure piston oil pump.
c) Automatic pull plate mechanism (for election)
2 Automatic pull plate system: hydraulic brake, tweezers chain drive, translation synchronization, tweezers chain pull manipulator.
2 The pulling plate system is composed of motor, hydraulic motor, pull plate trolley, sprocket, chain, etc. Under the control of the relay, the motor drives the hydraulic motor, and the left and right pull plate trolleys are driven by the chain to complete the pulling plate. The pulling plate system adopts intelligent control. The action when pulling the board is slow, fast and slow, which can improve the efficiency of the pull plate and protect the filter plate.
2 The pulling plate system is hydraulically controlled, and the pulling plate speed can be adjusted arbitrarily.
d) Filter components - van filter plates
2 The filter plate is made of reinforced polypropylene (PP) and has an overall variable cross-section design, which makes the flow resistance small and the flow rate fast.
2 It adopts special raw material formula and pressing process, and is equipped with a filter plate produced by a 1000-ton high-pressure hydraulic press. Its mechanical performance indexes are all above the national standard.
2 After the filter plate is molded, the surface of the filter plate is processed once by a special milling machine, so that the surface of the filter plate is flat and the thickness is uniform to ensure the sealing of the device, and the phenomenon of spraying is avoided during the filtration process.
2 The filter plate is made of reinforced polypropylene, which is resistant to acid, alkali, corrosion and has certain temperature resistance.
e) Hydraulic station components
2 Hydraulic system, hydraulic components are made by well-known domestic manufacturers. Due to the reasonable design, the hydraulic components have stable performance and reliable operation, so that the hydraulic station assembled and manufactured by our company not only has the characteristics of good pressure maintaining performance, but also has more than double the service life of ordinary products.
2 The valve block is the core of the hydraulic station. The hole burr of the valve block (which is left in the process of processing the valve block) is a hidden danger of damaging the hydraulic components. The hydraulic manifold of our factory is washed and washed by the acid block after processing. Air back blowing. After assembly, on the hydraulic operation test bench, after repeated test with oil pressure, the next process can be carried out, which greatly improves the life of the hydraulic components and the stability of the hydraulic station.
2 The cylinder block adopts 45# steel, which changes the traditional casting method of ductile iron, avoids the cold separation and shrinkage caused by casting, and improves the strength and safety of the cylinder.
2 The piston rod is made of solid tempered round steel and chrome plated.
f) Electrical control section
The electrical control box is a separate structure for external spray treatment, enabling remote control. The main electrical components adopt domestic famous brands, relay control realizes hydraulic compression, pressure keeping, return stroke, automatic pull plate unloading, and the operation safety is good. (Alternatively, PLC control can be configured according to user requirements)
Third, the product manufacturing process
1, the whole machine performance
1. 1 Filter press The whole filter chamber is tight. There is no injection at the pressing surface. Leakage caused by the capillary action of the filter medium is allowed at the pressing face, and there is no leakage at other seals.
1.2 The pressure-reducing parts of the filter press were pressed for 1.25 times with a pressing force of 1.25 times without cracks and obvious changes.
1.3 The noise power of the automatic filter press during air running is less than 80db. Ordinary filter press is less than 70db.
1.4 Hydraulic and pneumatic systems meet the following requirements:
A. The hydraulic system should meet the requirements of GB3766.
B. Pneumatic system should meet the requirements of GB7932
C. Hydraulic components should meet the requirements of GB7935
D. For the hydraulic pressing device, the sealing test shall be carried out with a pressing pressure of 1.25 times, and the pressure drop within 20 minutes shall not exceed 15% of the test pressure.
1.5 The clearance between the filter plates after pressing under the pressure without any padding is as follows:
A., filter plate size
B. Filter press with filter plate size ≥1000mm×1000mm is not more than 3.5 mm
1.6 Filter press control system, compression system, filter plate moving device, filter cloth cleaning device, flap device, etc. work flexibly and reliably.
2, the main components
2.1 Castings
2.1.1 The surface has been carefully cleaned, and there are no defects such as cracks, cold partitions and shrinkage holes that affect the performance.
2.1.2 Non-machined surface roughness Ra is less than 100μm.
2.2 Metal weldment
2.2.1 In addition to the net welding slag, oxide scale and splashing, the weld is smooth and smooth, and there are no defects such as cracks, pores and slag inclusions that affect the performance.
2.2.2 The mechanical properties of the weld shall not be lower than the base metal.
2.3 filter plate, diaphragm plate, compression plate, thrust plate
2.3.1 The filter chamber depth difference of the vane filter plate is ≤1.5mm.
2.3.2 The surface of the filter plate is smooth and flat without flash, burrs and shavings. The sealing surface has no defects such as scratches on the outer edge. There are no obvious defects such as wrinkles, pores and delamination at the sealing surface and the through hole. The surface and the inlet and outlet holes must be unobstructed.
2.3.3 The geometry of the filter plate meets the following requirements:
A, off-board size
Filter plate dimensions (mm) | Tolerance (mm) |
≥1000mm×1000mm | ±5 |
B. The parallelism of the sealing surface of the filter plate includes the flatness error requirement caused by the warpage deformation.
Filter plate dimensions (mm) | Tolerance (mm) |
≥1000mm×1000mm | 2.0 |
C. The deviation of the thickness of the filter plate is not greater than the deviation of the flatness.
D. The sealing surface roughness of the filter plate is not more than 6.3 μm.
2.3.4 Appearance quality of the filter plate The company adopts visual inspection, and the appearance and geometrical dimensions of the parts are inspected one by one, and sampling is not allowed. The thickness deviation of the filter plate of the same filter press is ±2 mm in the upper deviation and -3 mm in the lower deviation.
2.3.5 The roughness of the sealing surfaces of the filter plate, the pressure plate, the thrust plate and the feed plate is less than 6.3 μm.
3, appearance quality
3.1 The color of the whole filter plate is uniform.
3.2 The difference between the top surface and the side of the two adjacent filter plates of the whole machine is less than 3.0mm.
3.3 Filter plate filter surface small bump point cylinder damage meet the requirements of the following table:
Filter plate dimensions (mm) | Bump defect | Every defect point |
≥1000mm×1000mm | ≤5 | ≤8 |
3.4 The paint surface of the filter press is smooth, flat and firm without obvious flow marks and brush marks. The surface has no defects such as cracking, wrinkling, bubbles and particles.
3.5 In addition to special materials such as stainless steel, rubber and plastic materials, the parts have no paint outflow. The exposed surface is not exposed and is treated with anti-corrosion treatment.
3.6 Welds remove welding slag, weld skin and splash particles, and the surface of the casting is carefully cleaned.
Fourth, quality service commitment
1. The "three packs" of the whole product is a leap year.
2. Product quality is lifelong. During the warranty period, if the quality of the equipment is found, we will be responsible for the repair and replacement.
Used by us. Outside the warranty period, long-term tracking of equipment, help repair, matching, the cost of
The buyer will bear the burden and the supplier will only charge the cost.
3. During the production, assembly and trial production phases of the equipment, internships and training can be provided for the use of factory personnel.
4. Product acceptance, if there is shortage, damage, unqualified testing, etc., the supplier will deal with it within two days.
5. Received the equipment commissioning notice, dispatched the staff to guide the installation and commissioning within two days and provide training for the operators.
6. Received the equipment maintenance notice and dispatched the staff to the site for repair within two days. Outside the “Three Guarantees†period, only the cost is charged.
7. During the equipment overhaul, dispatch personnel to assist in handling.
8. Long-term preferential supply of spare parts and accessories.
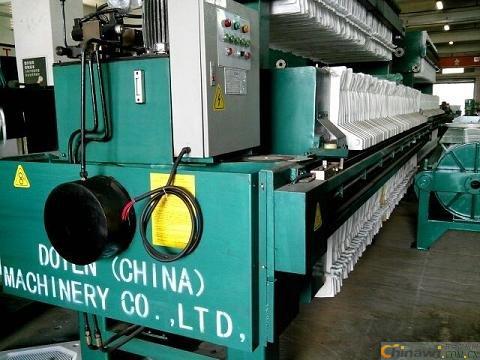
Ball Valve Stems & Seats,Floating Elbow Valve Spheres,Cast Elbow Valve Spheres,Cast Solid Elbow Valve Spheres
WENZHOU ZHENHONG VALVE BALL CO., LTD , https://www.zhvalveball.com