ã€China Aluminum Network】 Aluminum extrusion refers to the aluminum alloy high temperature casting billet into a special mold, under the pressure of the extruder to provide a strong force, according to the given speed, the aluminum alloy extrusion from the cavity , In order to obtain the desired shape, size and aluminum alloy extruded profiles with certain mechanical properties. Aluminum extrusion molding process is very complicated, in addition to the extrusion of circular and circular section aluminum profile is a two-dimensional axisymmetric problem, in general, other shapes of aluminum extrusion is a large three-dimensional flow deformation problem. Therefore, the quality of the extrusion die design and its service life become one of the keys to the economic feasibility of the extrusion process. Reasonable design and manufacturing can greatly extend the life of the mold, which is of great significance for improving the production efficiency, reducing the cost and energy consumption.
At present, China's profile extrusion die design basically remains in the traditional accumulation of engineering analogy and design experience. In fact, the more complex the profile section, the more pronounced the non-uniformity of the extrusion deformation, resulting in the new design of the mold is difficult to guarantee a uniform outflow of the billet, causing the profile due to twisting, waves, bending and cracks Defective and scrapped, the mold is also very easy to damage, must go through repeated trial mode, repair mode can be put into normal use, resulting in waste of funds, manpower, time, resources, etc. [1]. Therefore, with the continuous development of aluminum profile products to large-scale, flattened, thin-walled, highly refined, complicated and multi-purpose, multi-functional, multi-variety, long-life, improving the traditional mold design method has become the current The urgent needs of aluminum industry development.
1 Significance of Aluminum Profile Extrusion Die CAE Technology Aluminum Profile Extrusion Die CAE technology is a numerical value that uses the extruded product model established in CAD, combines extrusion process and control parameters, completes the analysis of its forming process, and optimizes the corresponding mold design. technology.
The specific approach is: based on the preliminary design of the extrusion die, according to a preliminarily prepared process test plan, using the computer to simulate the entire extrusion process, physical stress distributions such as stress, strain, temperature, and flow velocity in the extrusion body are obtained and squeezed. Pressure process conditions such as pressure, temperature, and speed are determined at each stage. The influence of mold sections such as the cross-section of the extrusion die and the diverter holes, weld cavities, diversion grooves, etc. on the flow of the formed aluminum is determined. The mold may appear during use. Deformation, collapse, chipping, cracking, wear, "sticking" and fatigue and other defects and their location; put forward analysis report and recommend suitable extrusion conditions to the designer, the designer then corrects the die design program according to CAE analysis results. After several iterations, until the mold design program meets product design requirements and product quality requirements [2]. This is actually the process of transferring the “trial-modification-testing†process at the production site to the computer to partially replace the time-consuming and costly test-work in the mold design and manufacturing process, thereby reducing the material and energy consumption at this stage. Reduce production costs and design high-quality aluminum extrusion dies.
Although CAE technology has obtained some successful applications in the field of aluminum extrusion die design and manufacturing, it is rarely applied to mold engineers. This is mainly due to the fact that CAE software has not been specifically developed for extrusion molding of aluminum profiles at home and abroad. Therefore, when mold engineers use some common or special CAE software (such as ANSYS/LSDYNA, MARC/AutoForge, Deform, etc.) to carry out mold design When analyzing the mold structure, in addition to requiring the user to have a solid extrusion process and extrusion mold design manufacturing expertise, and to be familiar with the working conditions of the extrusion mold components in the coupled field environment, he is also required to conduct numerical simulation techniques and The corresponding finite element analysis method must have a deeper understanding, which is more difficult for engineering and technical personnel working in the front line of production. This is one of the important reasons why CAE technology is not widely used in the extrusion die industry. .
The application of aluminum extrusion die CAE can shorten the design and manufacturing cycle of the die, improve the quality of the die, and enhance the market competitiveness of the enterprise. However, only by solving the above problems can CAE technology be widely used in the extrusion die industry. This is the significance of the aluminum extrusion die CAE technology research.
The current situation of optimization design of aluminum extrusion die Because it is a very complicated and difficult job to design a extrusion die with reasonable structure and economical practicality, therefore, extrusion workers in all countries in the world have theories and methods for die design (especially The optimization theory and method) carried out a lot of research work.
At the beginning of the development of extrusion technology, mold design was generally based on mechanical design principles using traditional strength theory combined with the designer's practical experience. With the development of elasto-plastic theory and extrusion theory, many new experimental theories and methods, computational theories and methods have begun to be used in the field of extrusion die design and fabrication. For example, engineering calculation method, metal flow coordinate grid method, photoelastic light-plastic method, dense grid pattern method, slip line method, upper limit element theory, and finite element theory are widely used in the determination of mold strain field and various The strength of the check, and then optimize the structure and process elements. With the development of computer technology, the CAD/CAM technology of extrusion die has been rapidly developed in the near 2030, and a large part of the technology is focused on the optimization of die design. He Delin et al.[3] developed a CAD/CAM system that can optimize the planar die and the splitter die using the IDEF0 method; Wang Mengjun et al.[4] used AUTOCAD120 as the graphics support environment and VISUAL BASIC4.0 as the development tool to develop the CAD. The system can effectively perform various calculations of the extrusion die, thus optimizing the design results; Yan Hong et al. [5] introduced the CAE concept into the die design process and pointed out the direction of optimization design; Liu Hanwu et al. [6] The concept of intelligent CAD was proposed to provide some ideas for the intelligent design of molds. In addition, researchers at home and abroad have used theoretical analysis, physical simulation and numerical simulation to analyze and test the deformation process, distribution and change of stress field and temperature field, friction and lubrication of aluminum extrusions. According to its research results, the extrusion die was optimized. For example, Zhao Yunlu and Liu Jingan [7] systematically discussed the optimization design of various extrusion dies. Some domestic researchers have used the finite element method combined with experimental methods to analyze and optimize the profile and mold structure of the extrusion die.
3 Development Status and Trends of Aluminum Extrusion Die CAE at Home and Abroad Numerical simulation of aluminum extrusion process can predict defects that may occur in the actual extrusion process, optimize the die structure design, adjust the extrusion process parameters and be targeted as soon as possible. Indicated technical solutions. Researchers at home and abroad have done a lot of work on this. South Korea's HyunWooShin et al. [8] performed a finite element analysis of non-axisymmetric extrusion processes in 1993. They used two-dimensional rigid-plastic finite element methods in combination with thick plate theory to simplify three-dimensional problems and performed the entire extrusion process. Without losing accurate numerical simulation, it also reduces the amount of calculations. For the deformation simulation, Yu Huping [9] used the plastic forming simulation software DEFORM, combined with the rigid viscoplastic finite element method function method to perform two-dimensional simulation of the extrusion deformation process of the plane diverter die, and obtained the aluminum alloy during the extrusion process. The distribution and changes of stress, strain, temperature, and flow velocity. Liu Hanwu et al.[10] used ANSYS software to perform finite element analysis and calculations on aluminum extrusions with split-flow composite die, and found structural defects that were not easily found in the original die design. Zhou Fei et al. [11] used a three-dimensional rigid viscoplastic finite element method to simulate the non-isothermal forming process of a typical aluminum profile. Three different forming stages of extrusion of aluminum profiles were analyzed, and the stress at each stage of forming was given. , Strain and temperature field distribution, and mold loading as a function of forming time throughout the forming process. For the pressure field, Yan Hong et al [12] used ANSYS software as a platform in 2000 to perform three-dimensional finite element simulation and analysis of the wall profile extrusion process, and obtained the displacement field, strain field, and stress field in the extrusion process of the profile. . It plays an important role in the selection of process parameters and the correction of the die structure size in the actual profile extrusion. For the friction and lubrication analysis of the extrusion process, in 1997, Russia's VadimL.Bereshnoy et al. [13] studied the technology of friction assist in direct and indirect extrusion of hard aluminum alloys. The development and application of this technology have greatly improved the production efficiency and quality. U.S. PradipK.Saha [14] studied thermodynamics and tribology in extrusion of aluminum profiles in 1998. He used thermodynamic numerical simulation to construct three different experimental models, analyzed the friction characteristics of the mold working zone and the flow metal contact surface, and also the temperature generated by the blank temperature and the heat generated in the extrusion process on the die working zone. The effect of the rise was verified by actual measurements. Studies have shown that the friction in the extrusion process has a direct effect on the accuracy and surface quality of the profile. The wear process of the die working zone depends on the thermodynamic properties during the extrusion process. The thermodynamic performance is again severely affected by the extrusion variables.
In terms of secondary development, some domestic research progress is also worthy of attention. Chen Zezhong and Bao Zhongyu[15] established an aluminum extrusion die CAD/CAE/CAM system based on UG and ANSYS through system integration and secondary development, and conducted CAD/CAE/CAM research on the split flow module. Effectively improve the mold design and manufacturing efficiency. Shenzhen University’s Li Jibin [16] wrote a program for the design of aluminum profile extrusion die parameters in C language, guided the design process of aluminum profile extrusion die in the form of a flow chart, and realized aluminum profile extrusion die in the form of human-machine dialogue. The optimal design of the parameters. Duan Zhidong of Lanzhou Railway Institute [17] introduced a strong finite element program in the ANSYS application program through the powerful front-end processing and solving function platform provided by ANSYS and introduced and summarized the secondary development of graphical user interface for ANSYS using UIDL. The general steps and laws provide useful help for the user to build up the corresponding graphical driver interface while expanding ANSYS functionality and establishing his own dedicated program. Sheng Wei [18] of Jiangsu Qishuyan Locomotive & Rolling Stock Technology Institute used ANSYS software as a platform to carry out the secondary development of metal plastic forming process simulation software, and applied the software to simulate the plastic forming process of forgings to improve the quality and prediction of forgings. The defects in metal forming and the development of reasonable processes provide a theoretical basis.
However, in general, these studies have focused more on theorization, and an extrusion die finite element analysis software that is truly suitable for common design and manufacturing personnel has not been available in China. Some secondary development also has great limitations in terms of specific applications. Therefore, it is imperative that the user-oriented research of the current finite element software be better applied to the design of extrusion dies.
4 Conclusions The improvement of aluminum extrusion die design and manufacturing standards is the key to improving product quality and enhancing market competitiveness, while aluminum extrusion die CAE technology plays an important role in the optimization of aluminum extrusion die design.
Domestic and foreign counterparts made use of aluminum profile extrusion die CAE to make beneficial attempts to optimize the aluminum profile extrusion die (including extrusion and extrusion processes), and achieved a lot of research and application results. This trend is worth noting.
Newer finite element analysis technology will be applied to the entire extrusion die design and manufacturing process as soon as possible, allowing more die engineers to master this optimized design method to improve the market competition of China's aluminum profile extrusion industry and its die manufacturing industry. force.
According to experience, the time used in each phase of CAE is: 40% to 45% for the establishment of the model and data input, 50% to 55% for the interpretation and evaluation of the analysis results, and the real analysis and calculation time only accounts for about 5% . CAE uses CAD technology to establish the geometric and physical models of CAE and complete the input of analysis data. This process is usually referred to as CAE preprocessing. Similarly, the results of CAE also require the use of CAD technology to generate graphical image output, such as generating contour maps of displacement maps, stress, temperature, and pressure distributions, and representing the color shading maps for application, temperature, and pressure distributions. We call this process For: CAE post-processing.
Philizon enjoys a high reputation in Grow Light and Aquarium Led Light fields throughout Europe and America, Philizon also insists on taking high technology to design the newest&best Square Grow Light and aquariumlight constantly as the market request. Our R&D team with more than 10 people has rich experience in appearance design, electronic structure,heat dissipation simulation analysis, optical lens design, lightcontrol system etc. Most of our hydroponics full spectrum led grow lighting and marine coral reef ledaquarium lighting are private modules,we have 10 more design patent and utility model patent till now.
Our Square Grow Light and LED Aquarium Light are popular in led market, cause its elegant outlook and its high quality and competitive price.
What is Full spectrum led chip ?
It is the newest trend for indoor plants. Advanced LED Grow Lights chip,not provide sigle color ,provide broad spectrum 400nm~840nm,simialr with sun light ,but most is red and blue,it is best for plant grow.This is a revolutionary step for Grow light which have previously been unable to act as the sole light source for the indoor garden.Suitable for all stages of plant growth.
Advtanges:
Upgraded Epistar chips,High Lumen,High penetration.
Plug with listed certificate safe to use.
The Plug you can choose
Ageing Test
Package
Our professional Square Grow Light are suitable for all the indoor plants and good for seeding, growth,flowering and fruiting stages of plants, increasing the harvest and Saving energy.
Our Quality Control systems
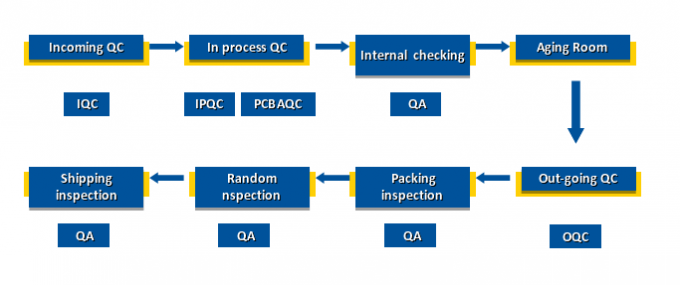
Our Company
Our Advantages
Professional: we are professional LED Grow Lights and LED Aquarium Light manufactuer here in China, you will get Professional and High quality LED Grow Lights and LED aquarium lighting from us and get good guarantee.
Cost-effective Price: we don`t have the lowest price, but the grow lights and aquarium light you get from us really cost-effective, good quality & decent price.
Win-win situation: Long term business is our mission, we think you will agree with us if you are running a business, so we will provide good led aquarium grow lights and warming service to build a long-term business relationship with you
24/7 unlimted customer service: we are always here for you for your question, any question just email us or call us, we will do our best to help you all the way.
Long term warranty: Don`t worry about the quality and we guarantee you 3years warranty for all the LED Plant Grow Light and coral reef led aquarium light..
Best buying experience: you will get the tiptop serive you have ever had,just have a try and you`ll see.
Trade Terms
Payment: T/T, L/C, Paypal, 30% deposits before production, 70% balance to be paid before deliverying(Western Union are welcome)
Sample will be delivered within 7 working days.
Discounts are offered based on order quanlityes.
MOQ:sample order are acceptable
Delivery ways:DHL,UPS,FedEx,TNT, door to door,by sea,by air,etc.
Philizon Square grow lights are perfect for green house applications and much more!
Led Grow Room Lights,Led Grow Living Room Lights,Led Grow Tent Room Lights,Led Green Grow Room Lights
Shenzhen Phlizon Technology Co.,Ltd. , https://www.szledplantgrowlights.com