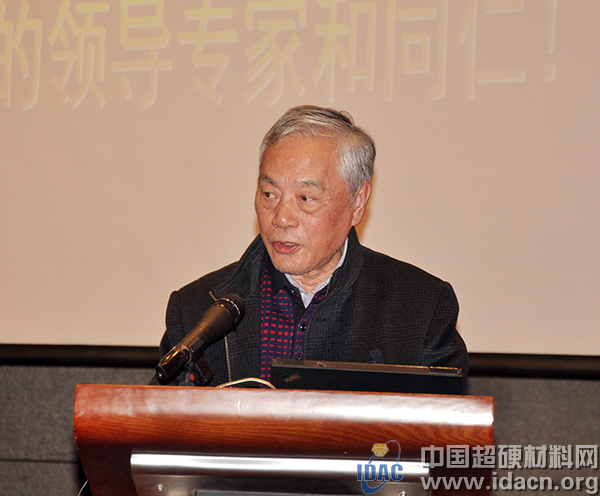
Lu Feixiong, an expert from Zhengzhou Abrasives Grinding Research Institute
At the end of 1963, after the historical success of the development of synthetic diamond in China, the research team continued to conduct a synthetic test for a period of time at Beijing General Motors. In 1964, I worked with the Jinan Casting and Forging Institute to undertake the "artificial diamond intermediate test" task issued by the Ministry of Machinery. The preliminary work of the “pilot test†was mainly carried out by Jinan, which was responsible for the design and processing of the hinged six-face press. During this time period, I established a superhard material test and a small production base. Including the super-hard material test room, equipped with a two-side press and small equipment for processing test pieces. Later, the first domestic six-sided top press was installed here; the physical and chemical room was responsible for the physical and chemical testing of the product, and also let out The laboratory is for the chemical treatment of synthetic products; the metalworking room arranges special machine tools and designs special fixtures to process the hard alloy top hammer; in order to process the pyrophyllite assembly parts, the special equipment is made, and the edge is improved, and the processing workshop is built outside the building. ..... All work up and down, work together, work together, overcome difficulties, and work hard for the development of super-hard materials. During this period, the scientific research strength has been strengthened and many new members have been added. With the use of the two-face top equipment, it is possible to continue the experimental research on synthetic diamonds and also train the team. When the “pilot test†entered the debugging stage of the hinged six-sided top press, most of the personnel of the research group were concentrated in Jinan, and together with the Jinan Casting and Forging Institute, the technical research in the trial operation of the hinge press was carried out. The remaining personnel, on the one hand, provide (or coordinate) logistics support for the front, such as test pieces, top hammers, etc.; on the other hand, continue to test on the two-face top equipment, prepare and carry out the synthesis test of cubic boron nitride.
The main participants in the cubic boron nitride test are Lu Feixiong, Xu Guotai, Yang Zhen and so on. In the process of developing synthetic diamonds, scientific and technical personnel have carefully collected and analyzed the technical materials published on foreign synthetic cubic boron nitride. The practical experience of successfully synthesizing diamonds is a reference for everyone to carry forward the spirit of self-reliance and glory for the country. Preparation, trial and error, finally in November 1966, on the 61 type ultra high pressure high temperature device, using magnesium powder as catalyst, hexagonal boron nitride as raw material, I took the lead in the successful synthesis of cubic boron nitride in China, after a period of time The verification test was transferred to the hinged six-sided top press to continue the test. The mass ratio of the hexagonal boron nitride and the magnesium powder, the synthesis pressure, the temperature and other parameters were optimized, and a relatively high synthesis conversion rate was achieved. The magnesium nitride catalyst synthesizes pale yellow cubic boron nitride. A process for separating cubic boron nitride from synthetic rods was obtained through experiments. The development work has progressed smoothly.
However, after the advent of cubic boron nitride, its application is not smooth. Cubic boron nitride is characterized by lower hardness than diamond, while thermal stability and chemical inertness to iron group metals are superior to diamond. At the same time, they were all very expensive materials at the time. As an abrasive, cubic boron nitride can only be used for difficult-to-machine materials, especially for difficult-to-machine metals and alloy materials. Unfortunately, at the time we did not have access to information on its industrial needs, and in the turmoil of the Cultural Revolution, it became increasingly difficult to obtain such information. Although a ceramic cubic boron nitride small grinding wheel was made in the factory, no suitable test object was found. In the end, it has to be compared with synthetic diamond. The same size of abrasive grains are processed at the high speed of the Nanjing Watch and Clock Component Factory. The efficiency is about half of that of the diamond. The drilling of the impregnated drill bit in the Lishui area of ​​Zhejiang Province, the efficiency and The life is also about half that of diamond. These test results do not reflect the characteristics of cubic boron nitride. As a last resort, the project was temporarily put on hold after the data was archived.
The social demand for cubic boron nitride occurred in the autumn of 1972. The three-machine department opened a science and technology coordination meeting in Kunshan, Jiangsu, and invited us to participate in one of the sub-items of “new high-speed steel grindingâ€. The background is that a large number of iron-based superalloys are used in aviation engines, high-speed steel knives for processing high-temperature alloys, and high-cobalt high-speed steels of the grade M42 are usually used abroad, and domestic cobalt resources are particularly scarce. In order to break the embargo embargo in Western countries, domestic steel mills have developed new high-speed steels represented by grades B201 and 5F-6, which are characterized by high vanadium content, good tool workability, but extremely poor wearability. . This situation directly affects the promotion and application of new high-speed steel tools. We feel that this may be an opportunity to break through the application of cubic boron nitride.
In 1973, we re-listed the topic and conducted a pilot study on the development of cubic boron nitride. The main members of the research group are Lu Feixiong and Yu Zhichao. The objectives of the project are to experimentally study the industrial production method of cubic boron nitride and the second to realize the application of cubic boron nitride in mechanical processing. In order to achieve the second goal, after close communication with the users, the research team took the prototype resin cubic boron nitride grinding wheel and tried it to the tool of Xi'an Hongqi Machinery Factory. At the scene, I saw an impressive boring boring tool for machining turbine discs. However, this time it is not a test grinding tool, but a test of the wearability of the new high-speed steel. On the tool grinder, try to grind the end face of the test finger with a dry grind. However, at the beginning of the trial grinding, the situation was very unsatisfactory. The grinding wheel could not grind the workpiece at all, and the amount of the infeed was reduced. The workpiece was very hot. Everyone's heart has sunk. However, the master who operated the machine did not stop, but slowly "squeaky" and wanted to see what happened. After two hours, I felt that the situation of trial grinding improved, and after about half an hour, the grinding became crisp and sharp. At this time, the master sighed, "The more the wheel is used, the better." The grinding wheel was removed and observed under a stereoscopic microscope. The shiny abrasive particles on the working surface of the grinding wheel were exposed. It turns out that the grinding wheel is not pre-trimmed, and the surface of the abrasive grain is covered with a layer of bonding agent. If it is a general steel, the binder is easily smashed and the tried-and-stick bar is hard and sticky, and the covered binder cannot be removed for a long time. The grinding wheel is reinstalled and the grinding is continued. The test rod wears off a one-centimeter wheel and maintains good grinding performance. At that time, everyone’s happy mood was hard to say. This is the result of the cooperation between the various professions and the division of labor and the use of the units! At this point, the early development of cubic boron nitride has been basically achieved.
A few days later, Hongqi Machinery Factory sent a team of 7 people to the office to report the test and communicate further cooperation. I was eager for military work, and the R&D work was fully rolled out. The development of cubic boron nitride grinding wheels for resin, ceramics and electroplated metals was arranged, and the research on the repair method of cubic boron nitride abrasive tools was arranged. During the development of these projects, the new high-speed steel tool products were finally processed. Cubic boron nitride abrasives have also achieved good results in processing high temperature bearing steels and high temperature alloys. Cubic boron nitride abrasives show a series of advantages such as high grinding capacity, high grinding ratio, long service life, high machining accuracy and good workpiece geometry retention. Cubic boron nitride and synthetic diamond are used as abrasives to process a variety of difficult-to-grind materials, showing a perfect combination of strengths and complements. In addition, based on the completion of the "development of cubic boron nitride", I have carried out research to improve the single production of cubic boron nitride and the development of cubic boron nitride polycrystals. At the same time of scientific research, it also engages in small production and promotes the transformation of scientific research results into realistic productivity. Cubic boron nitride and its products, at this time in my formation of a booming situation, won the National Science Conference Award in 1978.
This year marks the 50th anniversary of the successful development of cubic boron nitride in China. I was fortunate to have undertaken research and development in the field of cubic boron nitride for a long time after participating in the topic of “development of synthetic diamondsâ€, and devoted my own meager strength to its development. . The cubic boron nitride industry has grown from scratch, from weak to strong, especially in the past 30 years. With the deepening of reform and opening up, the promotion of the socialist market economy, the transformation of the system has ushered in the development of high-speed bases. Nowadays, the specifications of the products are complete, the production cost is greatly reduced, especially the rapid expansion of the production scale, which is impressive. I remember that in the mid-1980s, the annual output of cubic boron nitride in China was only a million carats. Now it is hundreds of millions of carats, and the growth is fast. China has become a big manufacturing country in this industry, and is now making the world a strong country. As product prices have fallen dramatically, those areas where conventional abrasives have traditionally been used have been or are being replaced by cubic boron nitride. Nowadays, cubic boron nitride has become an increasingly "popular" abrasive, and its popularity and application range have greatly promoted the technological advancement of machining and machinery manufacturing. Here, I wish that China's cubic boron nitride, especially the product industry, will achieve greater development on the road of reform and innovation. (This article is excerpted from the "Chinese Cubic Boron Nitride 50 Years Commemorative Collection", please do not reprint.)
used for machinery , automobile , bicycle ,furniture and components for other machines.
Cold Drawn Seamless Mechanical Tube (CDS) is a cold drawn 1020 steel tube. Produced from piercing hot rolled bar stock, the cold drawing process increases the tube's physical properties reducing the cost of machine time. Cold drawn seamless tubing provides a better uniformed OD and ID, enhanced machinability, increased strength, and tighter tolerances compared to hot finish seamless products.
Benefits of Cold Drawn Seamless Mechanical Tube:
Mechanical Tube
C45 bicycle part and auto part steel pipe
Liaocheng Xinglong Seamless Tube Manufacturing Co., Ltd. , https://www.lcxlpipe.com